The goal of any inking system is to place a uniform layer of ink across every dimension of the printing plate. The Lithographic process is unique in that it requires the ink form rollers to pass in contact with the nonimage areas of the plate without transferring ink to them.
All lithographic inking systems are made up of three main sections:
- Ink Fountain and ball roller
- Ink Distribution rollers
- Ink Form rollers
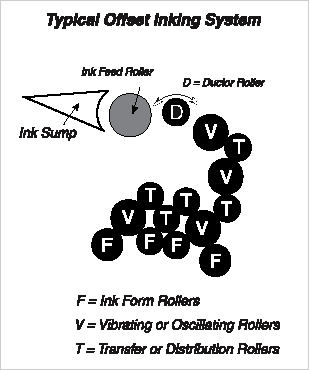
The ink fountain stores a quantity of ink in a reservoir and feeds small quantities of ink to the rest of the inking system from the fountain roller. The ink distribution rollers receive ink and work it into a semiliquid state that is uniformly delivered to the ink form rollers. A thin layer of ink is then transferred to the image portions of the lithographic plate by the ink form rollers.
The ink fountain holds a pool of ink and controls the amount of ink that enters the inking system. The most common type of fountain consists of a metal blade that is held in place near the fountain roller. The gap between the blade and the fountain roller can be controlled by adjusting screw keys to vary the amount of ink on the fountain roller. The printer adjusts the keys in or out as the fountain roller turns to obtain the desired quantity of ink. In simple presses, the printer must turn these screws by hand. The modern state of the art press today, the adjusting screws are moved by “servo” motors which are controlled by the printer at a press console. Thus the printer can make ink adjustments electronically. If the printer needs to increase or decrease ink in an area of the plate (print), he need only adjust the needed keys to allow more or less ink flow through the blade.
The ink distribution rollers spread the ink out to a uniform layer before it is placed on the plate. There are generally two types of distribution rollers:
- Rotating distribution rollers
- Oscillating rollers
The rotating distribution rollers rotate in one direction. The oscillating rollers rotate and move from side to side. Ink is transferred to the ink distribution rollers by a ductor roller. The ductor is a movable roller that moves back and forth between the ink fountain roller and an ink distribution roller. As the ductor contacts the fountain roller, both turn and the ductor is inked. The ductor then swings forward to contact a distribution roller and transfers ink to it. The rate of rotation of the ink fountain roller and the gap between the fountain blade and roller control the amount of ink added to the distribution system. Any roller on a press that contacts the plate is known as a form roller. An ink roller that touches the plate is an ink form, a water roller that touches the plate is a water form.
A simple indication of the quality of a printing press is the number of distribution and form rollers. The greater the number of distribution rollers, the more accurate the control of ink uniformity. It is difficult to ink large solid areas on a plate with only one form roller. With three (generally the maximum), it is relatively easy to maintain consistent ink coverage of almost any image area on the plate. Business forms presses, which print very little coverage, usually only have one or two ink form rollers. Because of this, they cannot print large solid or screen images. Smaller less sophisticated presses also have the same problem, however, many of the newer presses today are being equipped with larger better inking systems to meet the growing print demands of the consumer.
A whole battery of tests are run on every ink batch produced.
Fineness Of Grind
This is checked with an instrument called a grindmeter which is basically a wedge ground out of a stainless steel block. This wedge is 1 or 2 thousands of one inch deep at the deep end and graduates up to 0. An ink sample is placed in the trough and drawn down with a steel doctor blade. The presence of large particles will show up as scratches or specks in the trough after the doctor blade has been drawn down. Fineness of grind is critical for several reasons. First of all in order to gain the maximum efficiency from a pigment, the most expensive ingredient, it is essential that it be thoroughly dispersed. Secondly, a coarse grind can lead to premature plate wear or piling on the plate, thus causing printing problems.
Shade
There is more to formulating an ink than just loading the maximum amount of pigment in to it. The amount and type of pigment will have a drastic effect on the body, viscosity, flow characteristics, transfer characteristics, and water pick-up properties of the ink, in addition to the print density and trapping characteristics on the print. In process work shade is very important. If the inks are not the proper shade, the results from the press cannot be expected to match the original artist copy or the proofers preliminary print. Shade is checked by a draw down versus the standard.
Length
Length is a properly associated with the ability of an ink to flow and form filaments. Ink can be long or shore. Long ink flow well and form long filaments. They are undesirable especially on high speed presses because thy have a tendency to fly or mist. Short inks have the consistency of butter with poor flow properties. They have a tendency to pile on the rollers, plate or blanket. Most satisfactory inks are neither excessively long or short.
Tack
The tack of an ink is the force required to split a thin film of ink as it transfers down or up the ink train from roller to roller; roller to the plate; plate to the blanket; and blanket to the stock. The ink formulator will use an instrument called an Inkometer to measure the tack and will use this instrument to help him adjust the final formulation of the ink. The measure ink tack and the stability of ink tack an Inkometer is used.
Inkometer Stability
The ink formula must be balanced to obtain the best combination of fast, low temperature dry and good ink train stability. To check the inks tack and tack stability, ink measured on a inkometer is measured at 90?F at 1200 RPM. Some ink companies will measure ink at 90?F 900 RPM. Thus a ink measured at 1200 RPM with an ink tack of 16 will have an ink tack of 13 when measured at 900 RPM.
Viscosity
Viscosity is a measurement of the flow characteristics of a given ink and it determines the force required to move an ink down the ink train or to pump it through pipe lines. The instrument that we commonly use is the Laray or “falling rod” viscometer.This instrument can be used to measure the viscosity and the shortness ratio of an ink. The shortness ratio enables the formulator to measure the gel structure of an ink and to predict the performance of the ink in the fountain and on the ink train. It also is a valuable tool to monitor an ink from batch-to-batch to assure consistent quality.
Water Pick-up Percentage
In offset printing, the ability of the ink to interact with the fountain solution is critical; however, excess water pick-up can lead to emulsification which can show up on the print as loss of strength, enlarged dot, dull finish or poor rub.
Evaluation for Unground or Foreign Material
This test is conducted by mixing a sample of ink in a solvent and then filtering the residue on a fine mesh screen. The screen is then rinsed with solvent and dried. An observation is made of the foreign material. The operator must make a determination whether to accept or reject the batch based on the amount of this material.
Once the ink formula has been prepared in the lab and tested for proper physical properties, it can then be run through a battery of tests to determine its printability and performance after printing.
Ink Makeup
There are three properties of ink that control the ease and quality of image transfer:
- Viscosity
- Tack
- Drying quality (Coldset only)
Viscosity – is used to accurately describe the “body” of ink. Some inks are heavy (offset and letterpress) and some are light (flexographic and gravure inks). Viscosity, or resistance to flow, can be measured and is a term universally accepted in the printing industry.
Tack – is actually the “stickiness”. Tack must be controlled during the printing process in order to transfer images and deliver the sheet through the press. Tack can cause paper (especially coated paper) to stick to the blanket of an offset press. Ink that is excessively tacky may also pick the surface of the paper and cause misfeeding. Remember that to pick means to lift or tear small pieces of the paper뭩 surface. Tack will increase as one color is printed over another as it starts drying. When printing multicolor and process color (black, cyan, magenta and yellow) work, decrease the amount of tack on successive runs. The first printing unit should have the highest tack. Each successive printing unit should be printed with ink of less tack. In this manner the ink is “trapped” or transferred from the printing unit (image on the blanket) to the paper or ink on the paper.
For example, if we are printing black, cyan, magenta and yellow the black ink will contain the highest tack and yellow the lowest. As we first print black (highest tack) the ink begins to dry as soon as the ink is transferred from the blanket to substrate (paper). As the ink begins to dry, the tack increases. At the second printing unit, the cyan ink (which has a slightly lower tack) is transferred to the substrate and possibility onto the just printed black ink. Since the tack of the black ink is higher than the tack of the cyan ink, the cyan is “pulled” or “trapped” onto the higher tack black. As the cyan/black dries, it increases in tack which traps the magenta and so forth. This ability to “trap” is important. You will hear many printers and paper people talk about “backtrap” mottle or “backtrapping” problems. Some of this pheonomen is caused by the interaction of paper and ink.
Drying Quality – The final, and extremely important, property of ink is its drying quality. With sheetfed inks, there are two stages in the drying process.
Ink should instantly set or stick to the paper. When ink on the press sheet is set, it can be handled without smearing. If ink does not set as it is stacked in the delivery side of a press, the image will transfer to the bottom of the next sheet. This transfer of wet ink from sheet o sheet is called setoff.
Ink needs to harden. When ink has hardened, the vehicle (solvent) has completely solidified on the paper surface and will not transfer. The time it takes for liquid ink to harden to a solid state in called the drying time.
There are three methods for coldset ink drying:
- Oxidation
- Penetration
- Evaporation
Most sheetfed inks contain a drying oil (soy, linseed, cottonseed, etc.) which is hardened by a chemical process called oxidation. To oxidize is to combine oxygen with the drying oil which changes the vehicle of the ink from a liquid to a solid.
When an ink is printed on an absorbent substrate, drying results from a physical process called penetration. When ink dries by penetration, most of the vehicle is absorbed into the substrate. The ink vehicle is not changed to a solid state in this drying process. Inks that rely heavily on drying by penetration are not popular because the ink never hardens. Handling work printed with penetrating-drying ink usually results in ink transfer to the hands. Business forms and newsprint inks rely on this form of ink drying.
Some coldset inks dry by evaporation. Resinous and other film-forming solutions in the in vehicle pass off a vapor during the drying process. Drying by evaporation is much like drying by penetration. The volatile solutions disappear (by evaporating instead of penetrating), leaving an ink film on the surface of the substrate.
Most sheetfed inks use a combination of oxidation and penetration to accomplish drying. Heatset inks are far different from sheetfed inks. They dry by evaporation of the main solvents and setting the ink by the chill rollers. See the web offset section for a description of ink drying.
To assist in ink drying, additives can be added to the ink. These additives are “catalysts” which accelerate the oxidation process. The two main ink dryers used are:
Cobalt – a very powerful surface dryer,. Violet in color until oxidized where it will turn brown. This dryer tends to discolor whites. It is readily soluble in organic acids, so it may be affected by the fountain solution. Cobalt acetate can be dissolved and introduced into the fountain as a drying activator.
Manganese – is a “through-put” dryer with less vigorous catalytic action than cobalt. It is brown in color, has less effect on whites than cobalt and is unlikely to leach out by fountain solution.There are ways to calculate the amount of driers used in a ink. See Table 1 and 2 below for examples
Drier Calculations
Drier recommendations are based on percent metal on vehicle solids
To calculate the quantity of various driers required to be added to an ink formulation it is necessary to know, a) vehicle solids, b) percentage of metal available in the driers, and, c) required percentage of metal on vehicle solids
The quantities of driers is then calculated from the following formula:
Drier required (b) = Vehicle solids (lb) X % Metal required / % Metal in drier
Driers
Driers | Drier Based on vehicle solids |
Colbalt | 0.01 to 0.1% Metal |
Manganese | 0.02 to 0.0% Metal |
Lead | 0.35 to 0.5% Metal |
Calcium | 0.10 to 0.3% Metal |
Zirconium | 0.10 to 0.3% Metal |
Cerium | 0.10 to 0.3% Metal |
Zinc | 0.10 to 0.15% Metal |
XL-Dir* | 0.20 to 0.3% Metal |
* Shepherd Brand Drier |
A blend of the two drying additives, colbalt and mangenese for example, is usuallydded to allow for rapid surface drying (colbalt, to prevent set-off) and quickly harden the ink (mangenese, throughput drying). The printer will use a blend of these to accomplish this feat. The problem is, however, that there is a “window of opportunity” for dryers. To much will plastize the ink, and too little will slow drying. Generally, less than 1% (by weight) is used. There are today available other newer types of dryer additives that will enhance the inks drying ability even more. While most people think coated papers are more prone to drying problems, uncoated papers many times experiences greater drying problems. This is due to the fact that coatings are made to absorb the oils in the ink. Uncoated papers made with a very hard or tight surface will not absorb the oils easily resulting in slow ink drying. Care must be taken when printing these type of sheets. Drying can be easily accomplished by taking the precautions ahead of time. The printing, if printing on a tight uncoated sheet, should contact his ink supplier for recommendations on altering the ink. In most cases, a paper sample should be supplied to the ink company for this purpose. Uncoated papers vary greatly in their surface characteristics. Proper care in ink selection should be done. Newsprint, for example, is not Strathmore Elements. Ink will react completely different with these two types of paper!
As mentioned earlier, sheetfed or coldset inks dry mainly by oxidation and absorption. Many business forms ink, however, dry only by absorption. Oxidation is the process in which oxygen crosslinks with the oils and varnishes in the ink to form a solid. Absorption is the process of the solvent penetrating into the paper allowing the oxygen to interact with the oils and or varnishes.
Ink Setting – is the removal of the solvent from the ink film by absorption into the stock. This raises the viscosity of the ink and starts the surface drying. Setting the surface allows for backside printing, etc.
Ink Hardening (drying) – or total ink drying is accomplished over a longer period of time (up to 24 hours).
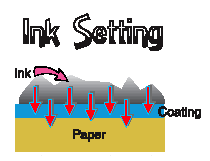
Solvents will separate from the ink and bleed into the coating or paper leaving the varnish on the surface to cross link with oxygen and harded. At first the surface of the ink will harden. This is known as setting.
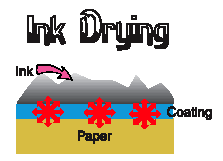
As oxygen cross-links with the help from driers, the ink over time will harden all the way through. This is known as total ink drying Solvents will separate from the ink and bleed into the coating or paper leaving the varnish on the surface to cross-link with oxygen and harden. At first the surface of the ink will harden. This is known as setting
Two of the main drying catalysts used to accelerate the ink drying process contain Cobalt or Manganese.
- Cobalt helps accelerate the surface drying process.
- Manganese speeds the internal drying.
The best recommendation one can give when printing a new type of paper is for the printer to consult with their ink supplier as to the proper amount as well as the maximum and minimum to use. Ink suppliers will take a paper sample and adjust the ink for drying properties or at least make recommendations to the printer on how to handle the drying process.